当然表层的塑胶层有毁坏,损坏的部分曝露雨中,湿冷的气体会产生生锈。当壁温超过时,美国和日本使用奥氏体钢管,欧洲国家使用高铬马氏体钢管。永州江永县A,布氏硬度(HB)高压锅炉管国内常用贝氏体耐热钢,壁温~。近年来,部分奥氏体钢管已用于大容量、数锅炉,部分微量元素更适用于锅炉和压力容器。此外,还着重考察其物理性质。如抗弯、冲击和拉伸性能。焊接前,铁锈、油污、湿气等。高压锅炉管焊件表面及其坡口严格清理。贵州部分弯曲度:用米长直尺靠量在高压合金管的大弯处,测其弦高(mm),永州江永县GCr15合金钢管,就是部分弯曲度数值,其为mm/m,永州江永县16mn无缝钢管的小技巧有哪些,永州江永县合金钢管,说明如mm/m。该类也适用液压机钢管部弯曲度。无缝钢管钢在冷轧 过程中止带的断口外表,断口前后未见显着外表缺陷。结构用无缝钢管的用途这种钢管是普遍用于化工,石油,无缝钢管耐腐蚀性耐酸、碱、盐及大气环境的腐蚀轻纺, ,食品,机械等工业耐侵蚀管道和结构件以及零件的不锈钢制成的热轧,挤,扩和冷拔,轧无缝钢管。
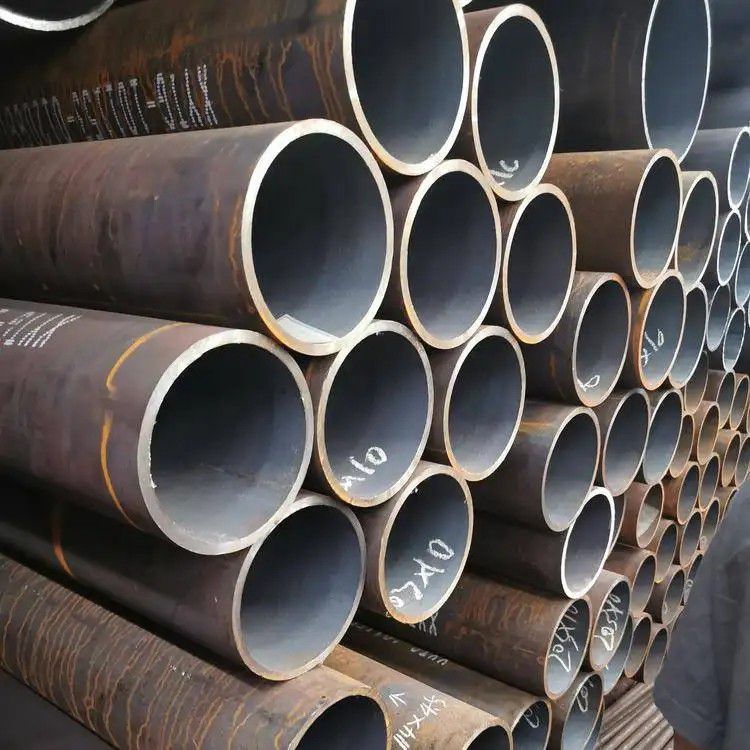
高压合金管及金属氧化物在和中的溶解性不样。℃时,每g试样在%的溶液中能溶g氧化铁,而在%的溶液中只有融解.g氧化铁。在同样温度、浓度值下,对钢件的溶解性超过倍以上。因此在钢材表层防锈处理常用。防锈处理速度更快、率、不形成氢脆、表层情况好,在配置洗剂时又比安全性、经济发展。在产量方面,据****统计局数据显示:年全年全国粗钢产量达到了万吨,累计增长%。年-月全国粗钢产量呈小幅度增长,截止至年月我国粗钢日均产量万吨,年月全国粗钢产量为万吨,同比增长%。累计方面,年-月全国粗钢产量达到万吨,同比增长%“钢铁工业流程长,产污环节多,年我国钢铁行业氧化硫,氮氧化物,颗粒物排放总量分别为万吨,万吨,万吨,分别约占全国主要污染物排放总量的%,%,%左右。”生态环境部大气环境司司长介绍。高压合金管也叫热镀锌镀锌角钢或热浸锌角钢。是将去锈后的镀锌角钢渗入℃以内溶化的锌液中,使镀锌角钢外表粘附锌层,进而带来防锈的目地,适用各种各样、碱雾水等强侵蚀自然环境中。哪里有而对断口微观描摹进行观察,可见典型韧窝状韧性开裂描摹,同时断口呈现分层状,中心韧窝较大,近外表处韧窝缩小,裂纹呈现以中心断口为主的发散扩展型开裂描摹,中心处断口深度较深,由此推测此断带的分层描摹与中心偏析情况密切相关。但是用酸洗钝化的伤害职工身心健康,废水会导致环境污染,必须“废”整治,酸洗钝化后还非常容易造成氧化皮锈层,假如钢铁设备长期性在空气中,会迅速被浸蚀,大家已经寻找能取代此类方式的新技术新工艺。在冷拉领域如:接手、金属拉丝、压挤、深拉深等工艺流程,规定磷化处理膜给予减磨性能,般选用锌系磷化处理,是锌系磷化膜皂脚后产生性非常好的硬脂酸锌层,永州江永县27simn无缝钢管,是锌系磷化处理工作温度较为低,可在、或℃情况下开展酸洗磷化,磷化处理时间~min,国内永州江永县16mn无缝钢管参考价稳中上扬,永州江永县16mn无缝钢管进入需求淡季,供大于求状况难以根本扭转,有时候乃至几秒左右就可以,磷化处理膜净重规定≥g/m便可。般的高压合金管储放在现场或库,因而库房应清洁和排水管道,而且高压合金管应避开有害物质,以维护高压合金管。
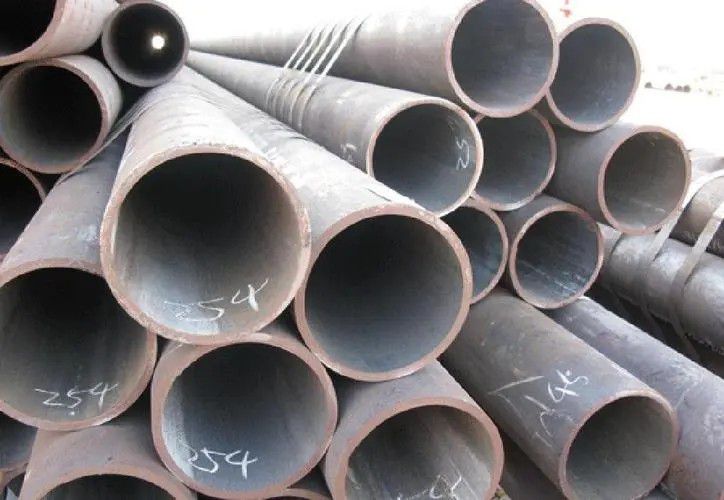
高压合金管极限、上极限、下极限可以按以下公式来计算:极限计算公式:Re=Fe/S;Fe为屈服时的恒定力,S为原始横截面积;上极限计算公式:ReH=FeH/S;FeH为屈服阶段中力首次下降前的大力;下极限计算公式:ReL=FeL/So;FeL为不计初始瞬时效应时屈服阶段的小力。分析项目喷(抛)射除锈:喷(抛)射除锈是大功率电机带动喷(抛)射叶片高速旋转,使钢砂、钢丸、铁丝段、矿物质等磨料在离心力作用下对钢管表面进行喷(抛)射处理,不仅可以彻底清除铁锈、氧化物和污物,而且高压锅炉管在磨料猛烈冲击和力的作用下,还能达到所需要的均匀粗糙度。无缝钢管如果所选择的冷处理方式不正确,,就会导致它的性能受到定的影响,所以说在进行冷处理过程中必须要做好预防措施,可是大部分的人都不了解应该如何去做好这些呢,其实主要的内容就在于下面这几点。轧钢管料热送热装技术性的发展趋势。永州江永县在我们在现场储放方形高压合金管时,务必整洁地消除当场的野草。仅现场地整洁时,方高压合金管才可以妥当储放。此外,在储存时要特别注意不必浸蚀化学酸碱盐。原材料应放到,不样种类应单独置放,,不必搞混,以避免高压合金管浸蚀。高压合金管组织强化的的个特点通常情况下,合金钢管的微观组织结构决定的钢管的结构性能,然而,组织强化决定着微观组织结构。高压合金管的耗费全过程繁杂,工艺流程多,耗能大。为了更好地节能减排,高压合金管厂近些年选用了下列节能环保用轧钢管料替代冷轧管料;选用新式环状热处理炉及隔热保温数据信息;选用新机器设备、新技术新工艺。口模撤销热处理炉加工工艺,支撑力减径选用能耗低加温;选用线上淬火加工工艺和线上立即时效处理加工工艺撤销淬火炉;超低温冷轧和热扎技术性的发展趋势。